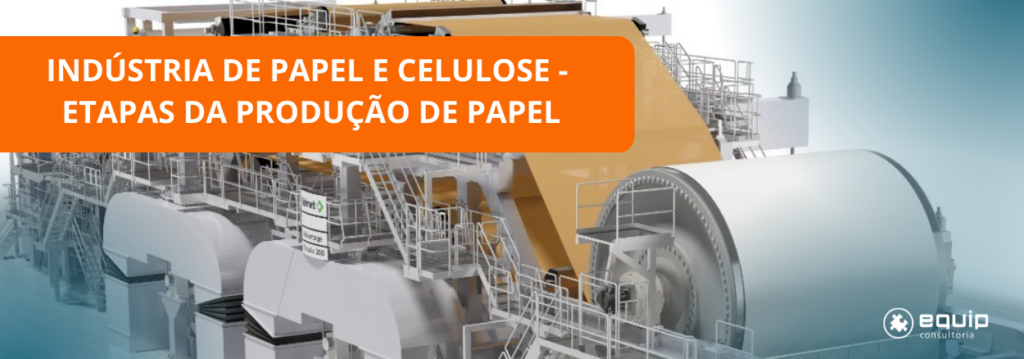
A produção do papel é caracterizada por uma longa rota de processos. Destarte, caracteriza-se como grande exemplo de uma indústria de processos químicos. O processo produtivo mais utilizado é o químico, com a utilização de reagentes que visam trabalhar na liberação das polpas de celulose a partir de altas temperaturas e pressão. A celulose é matéria-prima mais importante e principal constituinte do papel. Processada e pronta para a fabricação do papel, ela apresenta o aspecto ilustrado na Figura 1 a seguir:
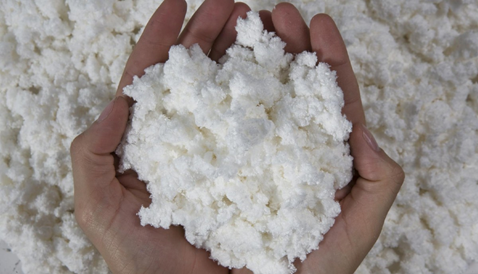
Entretanto, a massa de celulose pode receber características personalizada, com o objetivo de proporcionar o beneficiamento de diversos tipos de papel. A massa ilustrada na Figura 1 é conhecida como alvejada, haja visto que passou por processos de branqueamento, tal qual a deslignificação, que consiste na retirada da lignina, que confere a tonalidade parda. A celulose alvejada é aquela utilizada para fabricação de papeis brancos.
A massa parda apresenta tonalidade não alvejada. Assim sendo, é utilizada para fabricação de papeis com coloração mais escura. Ainda assim, é importante salientar que o processo de branqueamento não faz da celulose pronta para se tornar papel. O refino é extremamente importante para a adição de aditivos químicos que conferirão o produto almejado, como um papel absorvente, ou mais maleável, e até mesmo mais duro.
O processo de beneficiamento da celulose: o modelo kraft de produção
Os processos químicos podem ser ácidos ou alcalinos, e a escolha para o presente projeto visou o menor impacto ambiental possível. O modelo químico ácido possui como desvantagem a liberação da chamada “lama vermelha”, um rejeito altamente tóxico e prejudicial ao meio ambiente. Dessa forma, o modelo Kraft (alcalino) de produção do papel será o de referência para esse texto, haja visto que é o mais utilizado atualmente, pois possui ciclos curtos de cozimento comparado aos outros métodos, além da produção de pastas, isto é, polpas de alto rendimento.
A indústria papeleira utiliza eucaliptos e pinus como as principais matérias-primas para obtenção da polpa de celulose. As fibras vegetais são as mais utilizadas por serem renováveis, mais flexíveis e de menor custo. Além disso, o eucalipto e o pinus são árvores de rápido crescimento e, visto que o Brasil possui condições propícias ao seu cultivo, tais tipos são os mais utilizados no país. A Figura 2 a seguir apresenta uma plantação de eucalipto:
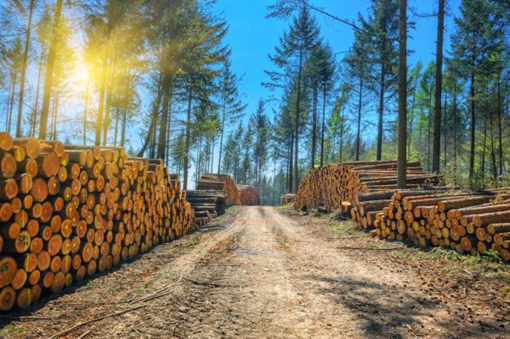
A priori, o processo se inicia na colheita. A expedição leva as toras à indústria. Logo, a madeira passa por processos de cominuição, como a trituração, com objetivo de transformar as grandes toras em pequenos pedaços. Os pequenos pedaços possuem maior superfície de contato e facilitam as reações de liberação da celulose, economizando reagentes e energia. Os cavacos (nome dado à madeira triturada) são submetidos à peneiragem, na qual eles serão separados com base em seu tamanho. O tamanho ideal do triturado é chamado de aceite. Os cavacos fora do tamanho ideal retornam ao processo por correntes de reciclo.
Ademais, os aceites seguem para o digestor. No equipamento, os pedaços de madeira são submetidos ao vapor d’água que irão facilitar no processo de cozimento. A seguir, o licor branco, constituído por hidróxido de sódio (soda caustica), NaOH, e sulfeto de sódio, Na2S, é adicionado aos cavacos. O cozimento segue em alta pressão e temperatura. A reação que ocorre em tal operação é dada por:
2 C6H10O5 + NaOH +Na2S à 2 NaC6H10O5S + H2O
A polpa resultante do cozimento é composta por lignina, celulose (C6H10O5), hemicelulose, hidróxido de sódio, sulfeto de sódio e água. Essa pasta é submetida à lavagem, que possui como objetivo separar a massa de celulose dos demais componentes da solução, que são solúveis em água. Os produtos dessa operação unitária são a massa parda e o licor negro.
É importante salientar que nem todas as outras fibras da madeira se separam da celulose e, haja visto que a lignina confere pigmentação parda, a massa recebe tal nome, mas, como a lignina e a hemicelulose não reagem, ponderar tais matérias orgânicas na reação é desnecessário. Além disso, é importante observar que a reação no digestor gera como produto o sulfito de celulose (NaC6H10O5S), principal componente da massa parda.
A massa parda segue para processamento em refinadores (e, caso desejado, para o alvejamento também), que possuem como objetivo garantir as características desejadas ao papel. O licor negro, por si, segue para a recuperação química, que é um processo extremamente importante para indústrias de polpa a papel, já que mais de 95% dos reagentes componentes do licor branco podem ser recuperados.
A recuperação química: uma planta análoga, mas essencial para indústrias de polpa e papel
A recuperação química começa com a concentração do licor negro. Tal solução é submetida à evaporação, com a respectiva evaporação da água. A seguir, o licor negro forte (ou concentrado), é queimado em uma caldeira, com a presença de oxigênio, na qual os sais de sódio são recuperados em uma pasta chamada de Smelt. A pasta supracitada é dissolvida em água e recebe o nome de licor verde.
A reação que ocorre em uma fornalha de recuperação química é a que está apresentada a seguir. É possível observar que a queima do licor negro forte possui como produto o carbonato de sódio (Na2CO3), que será utilizado na próxima etapa. Logo, a reação da formação da pasta supracitada pode ser representada por:
2Na2S + 4NaOH + 5O2 à 5Na2CO3 + 4H2O + CO2
A última etapa da recuperação química é a recuperação do hidróxido de sódio (CaO) no tanque de caustificação. Para que seja possível recuperá-lo, óxido de cálcio reage com água para formar hidróxido de cálcio (Ca(OH)2), como na reação a seguir:
CaO + H2O à Ca(OH)2
Após, o produto acima é colocado para reagir com o licor verde e formar soda, além do carbonato de cálcio (CaCO3), como demonstra-se na reação a seguir:
Na2CO3 + Ca(OH)2 à 2NaOH + CaCO3
Se o hidróxido de sódio for queimado, o carbono reage com o oxigênio, obtendo-se como produto o óxido de sódio, que é utilizado novamente na recuperação da soda, como observa-se na seguinte reação:
CaCO3 + O2 à CaO + H2O + CO2
Destarte, observa-se que a recuperação química é primordial, já que boa parte dos reagentes pode ser recuperador, inclusive a cal utilizada no processo de caustificação, que está dentro da planta de recuperação química. Sem a recuperação química a viabilidade de uma indústria de papel e celulose seria extremamente baixa.
Da celulose ao papel: dando forma e características ao produto
O processo de refino caracteriza-se como a última parte do beneficiamento da polpa para que ela se torne o papel. O refinador é um equipamento no qual as fibras são batidas para que possam ser adicionadas as cargas, colas e corantes, além de alume e resinas que darão as características desejadas ao produto. O batimento das fibras também faz o papel mais forte, mais uniforme, mais denso, mais opaco e menos poroso. Além disso, esse tipo de máquina provoca o máximo de desfibramento e de refinamento à polpa. É nesse momento em que a polpa pode ser branqueada, utilizando aditivos que garantirão cor branca ao produto beneficiado.
A conformação mecânica das fibras de celulose é o processo que procede o refino, e ocorre geralmente na chamada máquina a cilindro, que é um equipamento que possuiobjetivo continuar o tratamento da massa procedente de operações preliminares. Nessa etapa, a polpa é colocada em uma esteira vibratória com tela móvel. À medida que a tela avança, o movimento vibratório orienta parte das fibras e feltra com maior uniformidade a folha.
Ainda sobre a tela, as fibras passam por um processo de sucção para retirar o excesso de água na massa. Da tela, o papel é transferido para o primeiro feltro, onde há a remoção de mais água. Saindo do primeiro feltro, o papel passa por cilindros de aço de alisamento, de onde parte para uma série de cilindros de secagem, aquecidos internamente a vapor. Após a secagem, a massa passa pela calandra, equipamento que garantirá a superfície final do papel. Por fim, o papel acabado segue para ser enrolado em uma bobina. O papel sai da máquina a cilindro e é bobinado tal qual ilustra a Figura 3 a seguir:
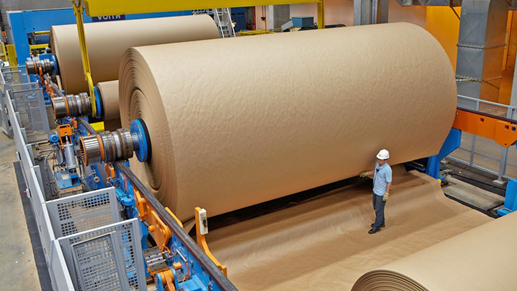
Dentre os três tipos de papel mais produzidos no Brasil, estão o papel branco e o papelão. Para o papel comum, a única diferença é que ele apresenta coloração alvejada, mas o processo da máquina a cilindros e do bobinamento, como ilustrou a Figura 3 acima, é o mesmo. Já para o papelão, faz-se necessário mais uma etapa de processamento.
O papelão é constituído a partir da colagem de várias folhas de papel pardo. Logo, sua expedição não pode ser realizada nos grandes rolos. Em tese, os papeis são colados com a formação de pequenas ondas entre as camadas, que garantirão resistência, principal característica do papelão. A Figura 4 a seguir mostra o papel utilizado para a formação do papelão:
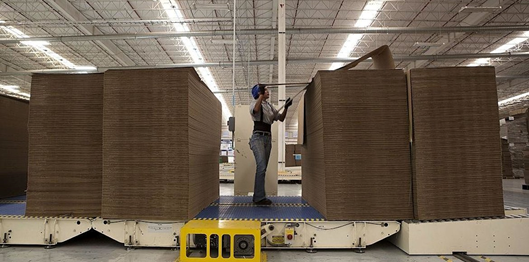
Sendo assim, o papel está pronto para expedição. Como supracitado, o papel pode ser transportado em grandes rolos ou cortados. A maneira de expedição varia de acordo com as características do papel e/ou necessidades do cliente que irá utilizar o papel comercialmente para diferentes finalidades.
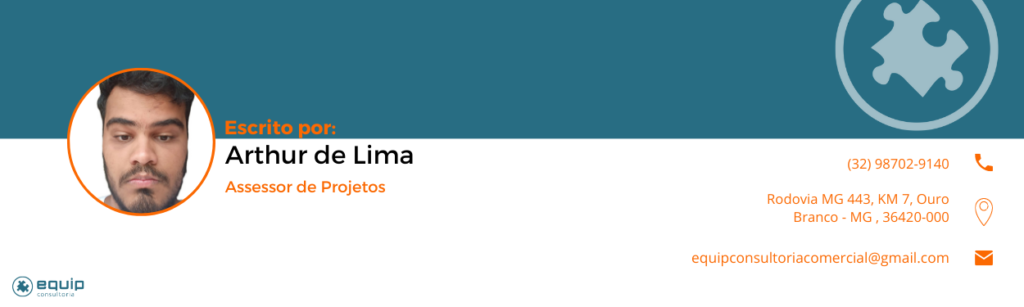