
O aço é um material essencial na sociedade moderna, encontrado em automóveis, arranha-céus e muitos outros objetos do dia a dia. Mas como transformamos o minério de ferro em aço? Vamos entender esse processo de maneira simples e clara.
Tudo começa com a mineração do minério de ferro, retirado da terra e triturado em pedaços menores. Os tipos mais comuns de minério de ferro são a hematita (Fe2O3) e a magnetita (Fe3O4).
Para ser usado na produção de aço, o minério de ferro precisa passar por um processo de redução. Isso ocorre em um alto-forno, onde o minério é misturado com carvão (na forma de coque) e calcário. O alto-forno opera a temperaturas altíssimas, acima de 1500°C.
Dentro do alto-forno, várias reações químicas acontecem. A mais importante é a redução do óxido de ferro pelo carbono. O monóxido de carbono (CO), produzido pela queima do coque, reage com o óxido de ferro, resultando em ferro metálico (Fe) e dióxido de carbono (CO2). O ferro produzido, chamado ferro-gusa, contém impurezas como carbono, silício, enxofre e fósforo.
Para transformar o ferro-gusa em aço, essas impurezas precisam ser removidas. Isso é feito em um conversor, onde o ferro-gusa é aquecido novamente e soprado com oxigênio. O oxigênio reage com as impurezas, oxidando-as e formando escória, que é removida. Esse processo, conhecido como conversão a oxigênio ou processo de Bessemer, reduz o teor de carbono e elimina outras impurezas, produzindo aço bruto.
Por fim, o aço bruto é ajustado para adquirir as propriedades desejadas. Isso pode envolver a adição de elementos de liga como cromo, níquel e vanádio, que conferem ao aço características específicas, como resistência à corrosão e maior durabilidade.
A transformação do minério de ferro em aço é um exemplo fascinante de como a química é aplicada na indústria. Combinando processos de redução, refino e ajuste de composição, transformamos materiais naturais em uma das substâncias mais versáteis e essenciais para a infraestrutura e tecnologia modernas.
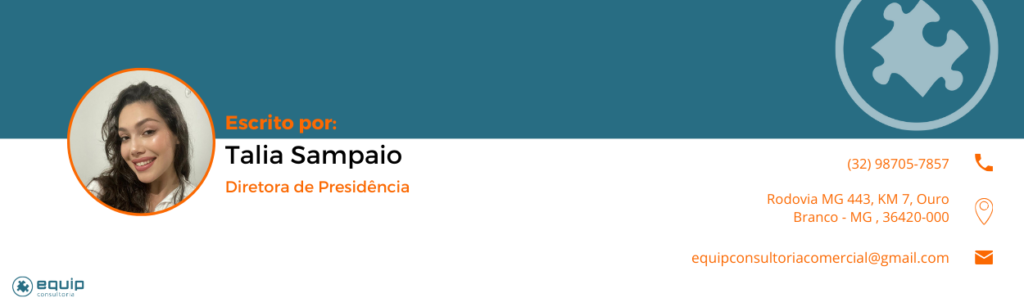